
ASHOK MUTTIN | AUGUST 5, 2020
How Did We Get Into This Mess?
How much of this sounds familiar?
Discussing chartering a plane from Shanghai to bring supplies to the US Checking the validity of the certificates produced by various middle-men at 3 am here in New Jersey Sending people to check the physical stock and seal it in the middle of the night in China Finding that letter of credit or price negotiation is out of the question, and don’t work anymore anyway Adding more than 100 unknown people to WhatsApp contact’s list because they have an “uncle and connections” in China and can help us with PPE supplies
Scrambling our data science team to develop a PPE estimator within 10 days to help our provider clients estimate the days of supply, and accordingly make a distribution to their front-line workers
If someone told me in the first week of March 2020 that we would be doing all of the above, my most likely response would have been “what have you been smoking lately?” But that’s exactly what we did. We threw all logic aside and chased every lead that claimed to help us with PPE supplies. We saw our clients challenged and decided to help in whatever way we could, all free of charge.
After innumerable hours checking the validity of suppliers and cross-referencing their credentials, we realized that the advantage had shifted entirely to them and we were at the mercy of what was available. Take it or leave it. And by the way, can you wire 100% of the money to China now?
While there is a lot of discussion on how we got here, the answers to us are fairly obvious and straight forward (how we acted on the numbers provided by the Chinese Government and built models accordingly is a story for another day):
1. Supply chain is not viewed as a strategic asset: If something goes wrong, it’s usually the supply chain team that is responsible for the mess, but it’s often clubbed by the administration spend bucket and gets scant attention, dollars, or importance if any. When was the last time you saw a supply chain leader on the board of any provider organization? Or in a corner office?
2. Under investments in the healthcare supply chain: Even though it’s the second-largest spend in provider organizations, there is very little investment to analyze supplier risks, build resiliency, hire and pay top talent, or invest in systems. Often times the argument is that it does not justify the ROI. Compare this to the number of investments that have gone into electronic medical records and electronic health records (mostly with disastrous results).
3. Extended supply chains: if you analyze many of the air disasters in the last two decades, you will notice they weren’t caused by engine failure alone; rather, there was a faulty nut, washer, bolt, small assembly, or other small parts that cost less than a dollar to make. Your supply chain is as strong as your weakest link, and in this case, our weakest links turned out to be PPE. Considering that these are consumables and had to compete solely on the basis of unit price, they have been outsourced to the cheapest manufacturer. And because of the consolidation in the industry, there are very few large manufacturers and even fewer here in the USA.
4. Resiliency and extensibility: Unlike other industries such as manufacturing or retail, the healthcare supply chain does not spend anywhere near the dollars or time in periodic supplier risk analysis. While everyone was caught off-guard with respect to PPE, a simple analysis would have shown that this supply chain is overly dependent on a handful of suppliers, none of the significant ones are on our shores, and there are capacity constraints arising out of countries acting out of their own national interests. None of this requires data science or machine learning and artificial intelligence.
5. Loss of core manufacturing base: While this is not the time or the place to debate about the benefits and challenges of outsourcing, it’s also a fact that existing manufacturers cannot very quickly re-orient their manufacturing capabilities and start producing PPE. As mundane as these products look, they still need raw materials, people on the assembly lines need training, customized shipping, packaging, and delivery. It’s the same case with food delivery as well; most meat manufacturers cannot re-size their restaurant-sized packages to cater to grocery chains easily. A national and international re-thinking needs to happen in terms of building strong, resilient, and flexible local supply chains in combination with global ones. And that raises its own questions:
Once the crisis is over, will we go back to business as usual and dismiss this pandemic as a once-in-a-lifetime event and hence not worthy of re-engineering? What is the true cost of thousands of lost lives? Will we continue to source from the lowest-cost supplier?
Will we factor in the total loss in terms of lives, jobs, income, and economic activity while arriving at the total cost of ownership?
Will we analyze our risks and take the “paranoid survive approach” and build contingency plans?
How will we bring a certain percentage of the supply chain within our borders and hence better manage risk?
How will we incentivize manufacturing at a state and national level?
How will we absorb the change in the costs?
Will this crisis lead to innovation in the manufacturing processes and hence neutralize the high labor costs? Without a doubt, these are some of the saddest days of our lives. We had anticipated a third world war, but this is much
worse than that, without a single shot fired. It would be wise for all of us in the supply chain to arm ourselves for the days ahead.
Safe and healthy.
More from SupplyCopia
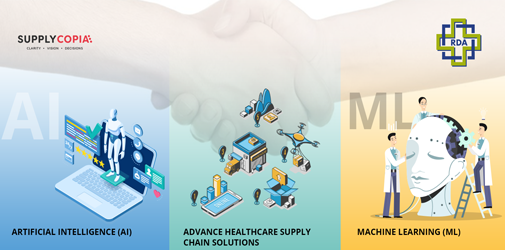
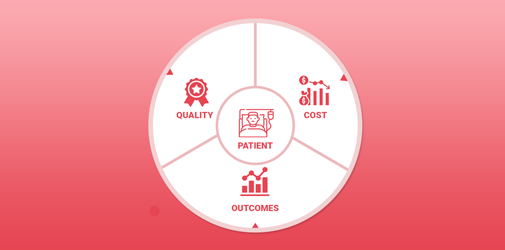